The Cutting Edge of Precision Machining Technology
In today’s world of modern manufacturing, precision machining technology has become an indispensable part of producing high-quality components and parts across various industries. From aerospace and automotive to medical devices and electronics, the demand for intricate and accurate machined parts is higher than ever before. This comprehensive guide will explore the fascinating realm of precision machining, shedding light on its processes, applications, and the vital role it plays in shaping our technological landscape.
Table of Contents
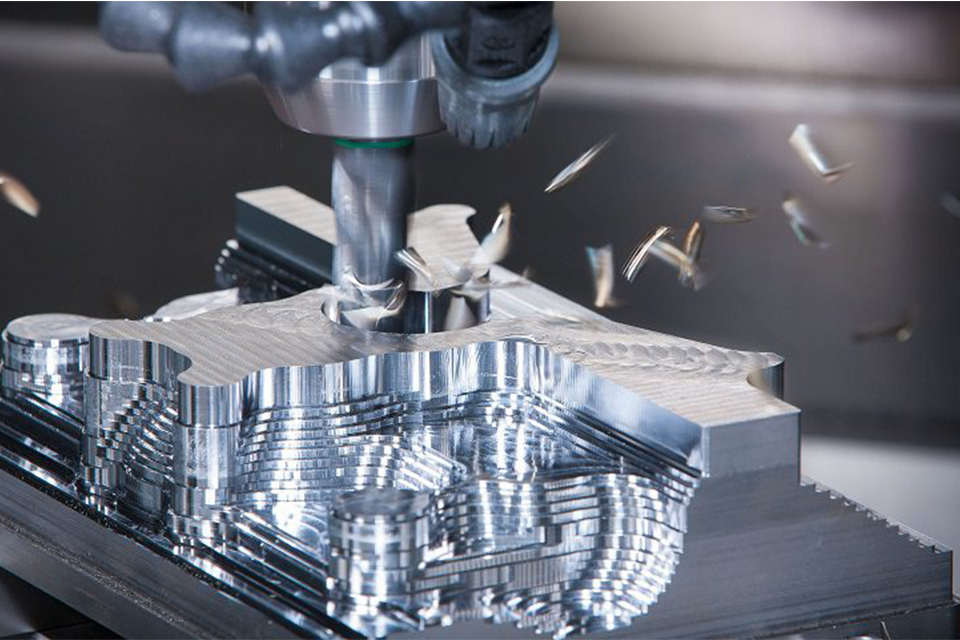
What is Precision Machining?
Precision machining, also known as precision cnc machining, is a manufacturing process that involves the removal of material from a workpiece to create highly accurate and precise parts or components. This process is driven by advanced computer numerical control (CNC) technology, which enables the precise control of machine tools such as mills, lathes, and drill presses. With CNC machining, complex designs can be transformed into tangible products with exceptional accuracy, often measured in thousandths or even millionths of an inch.
The Importance of Precision Machining
In the realm of modern manufacturing, precision machining plays a crucial role in ensuring the quality, reliability, and performance of various products. Many industries, from aerospace and automotive to medical and electronics, depend on precision machined parts to meet their exacting specifications. These high-precision components are essential for the proper functioning of critical systems, ensuring safety, efficiency, and durability.
Applications of Precision Machining
The applications of precision machining are vast and diverse, spanning numerous industries and sectors. Here are some notable examples:
Aerospace Industry
The aerospace industry heavily relies on precision machining to produce high-precision parts for aircraft engines, landing gear components, and structural elements. These machined parts must meet stringent safety and performance requirements, as even the slightest deviation can have catastrophic consequences.
Automotive Industry
In the automotive sector, precision machining is extensively used to create various components, such as engine parts, transmission components, and suspension systems. The tight tolerances and close tolerance finishes achieved through precision machining ensure optimal performance, fuel efficiency, and durability of vehicles.
Medical Industry
The medical industry demands the highest levels of precision and accuracy when it comes to manufacturing medical devices, surgical instruments, and implants. Precision machining is generally performed to produce these critical components, as even minor imperfections can have severe consequences for patient safety and well-being.
Electronics Industry
The electronics industry heavily relies on precision machined parts for various applications, including data storage devices, mobile devices, and audio equipment. The intricate designs and miniaturization of electronic components require machine tool calibration and precise machining to ensure optimal performance and reliability.
The Precision Machining Process
The precision machining process typically involves several stages, each contributing to the overall accuracy and quality of the final product. Here’s a general overview of the steps involved:
- Design and Planning: The process begins with computer-aided design (CAD) software, where the part or component is designed and modeled digitally. This digital blueprint serves as the basis for the subsequent machining operations.
- Material Selection: Depending on the application and requirements, a variety of materials can be used in precision machining, including metals, plastics, composites, and ceramics.
- CNC Programming: The CAD model is converted into computer-aided manufacturing (CAM) instructions, which are then translated into CNC programs that control the movements and operations of the CNC machining equipment.
- Setup and Tooling: The appropriate machine tools, such as CNC mills, lathes, and other specialized equipment, are prepared for the machining process. Cutting tools, fixtures, and workholding devices are carefully selected and installed to ensure precision and repeatability.
- Machining Operations: The CNC programs are executed, and the machining operations commence. Depending on the complexity of the part, multiple machining operations may be required, such as milling, turning, drilling, and grinding.
- Quality Control: Throughout the machining process, various quality control measures are implemented to ensure that the machined parts meet the required specifications. This may involve dimensional inspections, surface finish measurements, and material testing.
- Post-Processing: In some cases, additional post-processing operations may be required, such as heat treatment, surface finishing, or coating applications, to enhance the properties or appearance of the machined parts.
The Skilled Precision Machinist
While CNC technology plays a pivotal role in precision machining, the expertise and skills of the precision machinist are equally crucial. These skilled professionals are responsible for programming and operating the CNC machines, selecting the appropriate tools and cutting parameters, and ensuring that the machining process is carried out with the highest level of precision and efficiency.Successful precision machinists possess a deep understanding of machining principles, material properties, and cutting tool geometries. They must also have excellent problem-solving skills to troubleshoot any issues that may arise during the machining process.
Education and Training
To land a career as a precision cnc machinist, individuals typically pursue specialized training programs or associate of applied science degrees in manufacturing technology or machining. These programs provide hands-on experience with various CNC machines and equip students with the necessary knowledge and skills to excel in the field of precision machining.
The Future of Precision Machining
As technology continues to advance, the demand for precision machined parts is expected to grow across various industries. The integration of advanced manufacturing techniques, such as 5-axis CNC machining, accelerated CNC machining, and even high-speed robotics, will further enhance the capabilities and efficiency of precision machining processes.Additionally, the adoption of Industry 4.0 principles, which involve the integration of advanced technologies like the Internet of Things (IoT), Big Data, and Artificial Intelligence (AI), is poised to revolutionize the precision machining industry. These technologies will enable real-time monitoring, predictive maintenance, and optimized production processes, leading to higher productivity, reduced downtime, and improved quality control.
In Conclusion
Precision machining technology is a vital component of modern manufacturing, enabling the production of intricate and highly accurate parts that are essential for countless applications across diverse industries. As technology continues to evolve, the demand for precision machined components will only increase, driving further advancements in machining techniques, materials, and processes. Whether you’re an engineer, a manufacturer, or a consumer, the impact of precision machining is all around us, shaping the products and technologies that enhance our daily lives.
Key Takeaways
The future of precision machining lies in the integration of advanced manufacturing techniques, Industry 4.0 principles, and emerging technologies like AI and IoT.
Precision machining is a manufacturing process that removes material from a workpiece to create highly accurate and precise parts or components using advanced CNC technology.
It plays a crucial role in ensuring the quality, reliability, and performance of various products across industries like aerospace, automotive, medical, and electronics.
The precision machining process involves several stages, including design, material selection, CNC programming, machining operations, and quality control.
Skilled precision machinists with expertise in machining principles, material properties, and cutting tool geometries are essential for successful precision machining operations.
Frequently Asked Questions
What is the difference between conventional machining and precision machining?
Conventional machining methods are typically used for producing parts with standard machining tolerances, while precision machining is employed when a higher degree of accuracy and tighter tolerances are required, often measured in thousandths or even millionths of an inch.
What materials can be used in precision machining?
Precision machining can be performed on a variety of materials, including metals (such as aluminum, steel, and titanium), plastics, composites, and ceramics, depending on the application and requirements.
How does precision machining ensure quality and accuracy?
Precision machining relies on advanced CNC technology, precise machine tool calibration, and skilled machinists to ensure that the machined parts meet the required specifications and tolerances. Quality control measures, such as dimensional inspections and surface finish measurements, are also implemented throughout the process.
What industries rely on precision machined parts?
Precision machined parts are essential in various industries, including aerospace, automotive, medical, electronics, industrial equipment, power tools, and many others where high-precision components are required for optimal performance and reliability.
What skills are necessary for a career in precision machining?
Successful precision machinists must possess a strong understanding of machining principles, material properties, cutting tool geometries, and CNC programming. They should also have excellent problem-solving skills, attention to detail, and the ability to follow precise specifications and blueprints.