The Magic of Metal: An Introduction to Powder Metallurgy
The world of manufacturing is constantly evolving, and powder metallurgy stands out as a transformative technology. This process, which involves creating metal parts from powder, might sound like something out of a science fiction movie, but it’s a well-established manufacturing process with many applications. This article will introduce you to powder metallurgy, explaining how it works and highlighting its incredible capabilities. We will explore the entire process from powder production to the final metal part, making it clear why this method is essential to many industries. Understanding powder metallurgy will give you an idea of the hidden technology that shapes everything from cars to machinery. This is a worthwhile read because it offers a straightforward guide to a complex topic, offering practical examples, and highlighting the importance of this method in modern manufacturing.
Table of Contents
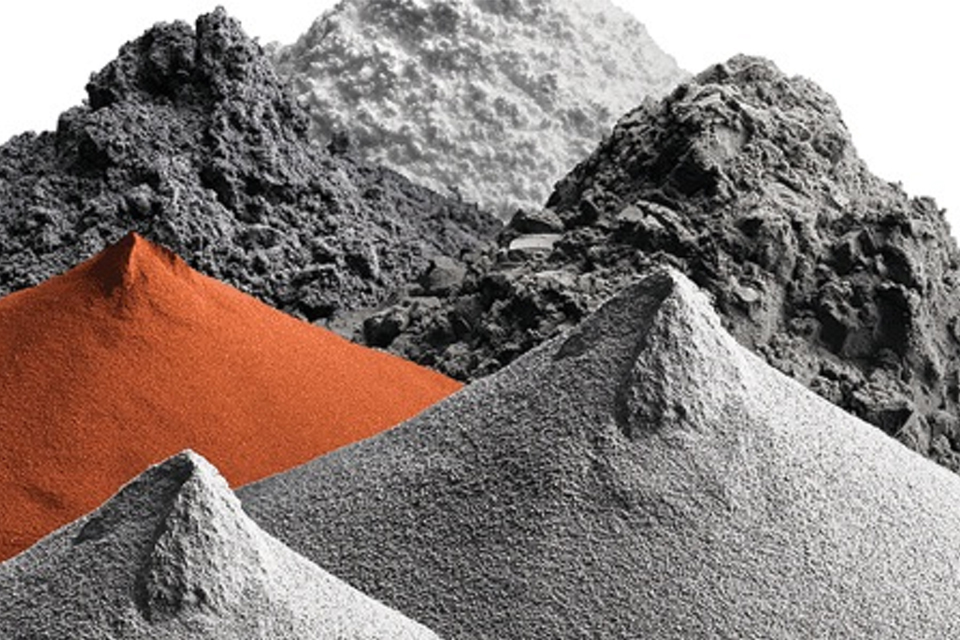
What Exactly is Powder Metallurgy?
Powder metallurgy (PM) is a manufacturing process where metal parts are created from metal powder. Instead of metal being melted and poured into molds, as in traditional casting, powder metallurgy utilizes a series of steps involving powder, compaction, and sintering. The basic idea is that by pressing together small particles of metal powder, you can create a solid metal part with a desired shape and properties. It’s a bit like making a sandcastle, but with metal and a lot more precision.
The powder used in powder metallurgy can be made from various metals, such as steel, alloy, or even ceramics. The resulting metal powder is then mixed with a lubricant to aid the compaction process. The mixture is then pressed into a desired shape, called a compact, using a die press. This compact, though having the correct shape, is still relatively weak. So, the compact is then heated to a high temperature, but below the melting point of the metal in a sintering furnace to sinter the powder together, forming a strong, solid metal part. This entire process allows the creation of components with specific and controlled properties.
How Does Powder Production Impact the Process?
The characteristics of the starting powder are extremely important in powder metallurgy because they have a huge impact on the quality and properties of the final metal part. There are many methods used for powder production, and the choice of method depends on the desired characteristics and the type of metal. One common method is atomization, where a stream of molten metal is broken down into fine droplets using high-pressure gas or liquid. These droplets then solidify into metal particles.
Another method involves chemical reactions to produce the powder, while others involve mechanical grinding of metal. The size, shape, and composition of the powder particles can all be tailored depending on the desired final product. For instance, the size of the metal particles impacts how well they can fill the die during the compaction phase, and also how the finished product will perform. The specific method of powder production plays a critical role in determining the final mechanical properties of the metal part. A better understanding of powder technology is very important for manufacturers, enabling them to control the quality and properties of their products.
What Happens During Compaction in Powder Metallurgy?
Compaction is a critical stage in the powder metallurgy process. It’s where the loose metal powder is pressed into a specific shape, forming a compact. The compaction process is generally performed using a die press where the powder is placed in a die, and then the powder is compressed using a hydraulic or mechanical press. During the compaction, the metal particles are forced close together, creating inter-particle contact.
During this process, the powder is subjected to high pressure, typically at room temperature. The pressure forces the metal particles together, creating a “green” compact that has the desired shape. The strength of the green compact is relatively weak, and this compact is then carefully removed from the die and taken for the sintering process. The goal of compaction is to achieve sufficient density and shape fidelity in the green compact. Different compaction methods, such as cold isostatic and hot isostatic pressing, can be used to achieve higher densities.
What is the Role of Sintering in Powder Metallurgy?
After compaction, the “green” compact is still weak and porous. To create a strong, solid metal part, it must undergo sintering. Sintering involves heating the compact to a high temperature, just below the melting point of the metal. This high temperature causes the metal particles to bond together, increasing the strength and density of the final metal part.
The sintering process does not involve melting the metal entirely. Instead, the metal particles fuse at their contact points, forming a network of solid metal. During sintering, the powder particles begin to diffuse, and the open voids and porosity in the compact are reduced. The final properties of the metal part, such as strength and hardness, are directly affected by the sintering temperature, duration, and the sintering atmosphere. Different sintering techniques can be used, including conventional furnace sintering, hot isostatic pressing, electric current assisted sintering, and plasma-activated sintering.
What Are the Advantages of Powder Metallurgy?
Powder metallurgy offers many advantages compared to traditional manufacturing methods. One key advantage is its ability to create metal parts with complex geometries and fine details, which would be challenging or impossible using conventional techniques. This allows for the creation of very intricate parts in a single process. Also, powder metallurgy can be more cost-effective for high production runs of complex parts because it reduces the need for secondary machining. It is powder metallurgy is a cost-effective manufacturing process.
Another advantage is the ability to control the material properties of the final part. By carefully selecting and blending the powders, it is possible to create alloys with specific desired properties. Also, powder metallurgy can be used to produce porous materials, which are useful for applications such as filters and bearings. Furthermore, the powder metallurgy process can lead to very little waste because most of the powder is used in creating the final product. In the automotive industry, for instance, powder metallurgy is used to create parts such as gears and connecting rods. These metal components also need to be able to withstand the high stress and temperatures that they are subjected to. In the same industry, powder metallurgy is used to produce parts for electric vehicles.
How Does Powder Metallurgy Compare to Forging and Casting?
When looking at different manufacturing methods, it’s important to understand how powder metallurgy stacks up against forging and casting. Forging involves shaping metal using compressive forces. While forging produces strong and durable parts, it may not be suitable for creating parts with intricate shapes, as it requires significant secondary machining. Casting, on the other hand, involves pouring molten metal into a mold. While casting can create complex shapes, it often results in parts with lower dimensional accuracy and higher porosity, which is a major disadvantage of casting.
Powder metallurgy combines the benefits of both forging and casting. It can produce parts with complex geometries like casting, but also with better dimensional accuracy and controlled material properties. While forging produces stronger parts, powder forging, a special version of the powder metallurgy process that combines features of both forging and the conventional powder metallurgy process, can help bridge that gap. In many cases, powder metallurgy provides a more efficient and cost-effective manufacturing process compared to these competing manufacturing methods. Also, this process is more flexible than casting. Powder metallurgy also allows for a continuous process, which can help with increasing production numbers.
What are Some Common Applications of Powder Metallurgy?
The use of powder metallurgy can be seen across many different industries. The automotive industry uses powder metallurgy extensively to produce gears, connecting rods, and other engine components. The aerospace industry also relies on powder metallurgy to produce parts for aircraft engines, and these components need to be able to withstand the high stresses and temperatures they are subjected to. In the aerospace industry, powder metallurgy is often used to create strong, lightweight metal parts. You can also explore how we are contributing to this industry by providing specialized NdFeB magnets for the aerospace sector at our page on custom NdFeB for aerospace.
Powder metallurgy is also used in the production of cutting tools, bearings, and electrical contacts, as well as a variety of other parts for other industries. The versatility of powder metallurgy has led to its wide adoption in many different industries. There are several other applications that are less commonly known. For example, powder metallurgy is also used to produce soft magnetic materials, such as those used in transformers. Also, the powder metallurgy process is used to create porous parts, which can be used as filters. Metal injection molding, a variation of the powder metallurgy process, allows for the creation of very precise and small parts, which can also be very complex. You can also use our custom design option for specific applications. The customized ndfeb magnets that we produce often go into such components. Consider also how these components enhance efficiency in areas such as wind power generation.
What Are the Future Trends in Powder Metallurgy?
The future of powder metallurgy is extremely promising, and there are many areas of ongoing research and development that are aimed at improving existing powder metallurgy technology. One area is the increased use of additive manufacturing or 3D printing with metal powders, and this is quickly becoming a very popular option. Metal additive manufacturing allows for the creation of very complex and customized metal parts. Also, additive manufacturing allows for the creation of parts with shapes that would not be possible using any other method. This has opened up many avenues for research and development.
Another trend is the development of new materials and alloys that can be processed using powder metallurgy. Also, research is aimed at improving the sintering process, to improve the quality and properties of the final product. This includes techniques such as hot isostatic pressing, which can achieve higher densities in the final part. The development of new materials with superior performance opens up opportunities for the aerospace industry and other sectors. Furthermore, the focus is on creating more sustainable and green technology in powder metallurgy, to reduce waste and energy consumption. In many cases, powder metallurgy is already more environmentally friendly than traditional manufacturing methods, but the push is to continue to make it even greener. Our expertise also extends to creating NdFeB magnets that support environmentally friendly solutions. For example, the motor magnet we produce are used in a range of applications, such as industrial motors used in the manufacturing sector, contributing to more efficient systems.
FAQs About Powder Metallurgy
What is the main advantage of using powder metallurgy?
The main advantages of powder metallurgy include its ability to produce complex shapes, its cost-effectiveness for high production runs, and its ability to control material properties.
What metals can be used in powder metallurgy?
Many metals can be used in powder metallurgy, including steel, aluminum, copper, titanium, and various alloys. You can also use ceramics.
What is the purpose of sintering in powder metallurgy?
Sintering is a heat treatment process that causes the metal particles to bond together, increasing the strength and density of the metal part. The sintering temperature is very important, as it must be lower than the melting point of the metal.
Is powder metallurgy a cost-effective manufacturing method?
Yes, powder metallurgy can be a very cost-effective manufacturing method, especially for high production runs of complex parts. It can reduce the need for secondary machining and also reduces waste.
Can powder metallurgy be used for large parts?
While powder metallurgy is more commonly used for smaller parts, it can also be used to produce larger parts using techniques such as hot isostatic pressing, and powder forging.
What are some limitations of powder metallurgy?
Some limitations of powder metallurgy include difficulties in creating parts with undercuts, limitations on the size of parts, and the need for specialized equipment. However, continuous advancements in powder metallurgy are addressing these limitations. Also, you should always consider your dimensional tolerances when designing metal components for production.
Summary
- Powder metallurgy is a manufacturing process that creates metal parts from metal powder.
- The powder metallurgy process involves powder production, compaction, and sintering.
- Powder characteristics are very important to the quality of the final part.
- Compaction involves pressing the powder into a specific shape, called a compact.
- Sintering is the process of heating the compact to bond the powder particles together.
- Powder metallurgy offers several advantages, including the ability to create complex shapes and control material properties.
- Powder metallurgy is often more cost-effective than forging and casting for certain types of parts.
- Powder metallurgy has various applications, including the automotive and aerospace industries.
- Future trends in powder metallurgy include the increased use of additive manufacturing and development of new materials for the process.
I hope this introduction to powder metallurgy has been both informative and engaging. The use of powder metallurgy is quickly increasing as manufacturers become more aware of its many benefits. If you have any further questions, please feel free to reach out. We specialize in producing NdFeB magnets using a highly refined powder metallurgy process, tailored to meet your specific industrial needs. To learn more, explore our site and consider how our custom NdFeB magnets can enhance your applications. If your application requires unique magnetic properties, our magnet coating options might be just what you need. We also offer a variety of magnet grades to best suit your needs.