The Production of NdFeB Magnets and How They Shape Modern Technology
Understanding how these magnets are made provides insight into their importance in industries like automotive, renewable energy, and electronics. This article explores the step-by-step production process, the materials involved, and the future of NdFeB magnet manufacturing. Whether you’re a professional or a curious reader, this guide will help you appreciate the science behind these powerful magnets.
Table of Contents
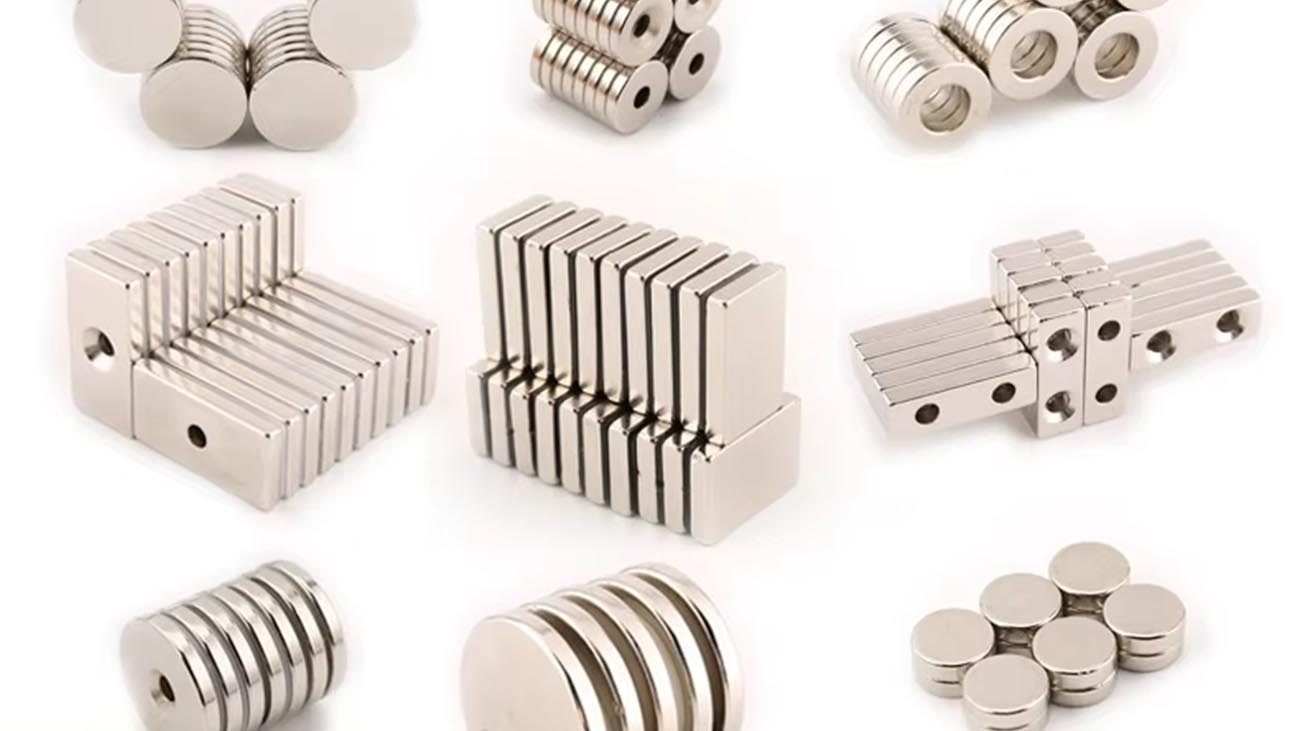
What Are NdFeB Magnets?
NdFeB magnets, short for neodymium-iron-boron magnets, are a type of rare earth magnet known for their incredible strength and versatility. They were first developed in the 1980s as a cost-effective alternative to samarium cobalt magnets. These magnets are widely used in applications requiring compact size and high magnetic field strength, such as electric motors, wind turbines, and medical devices.The unique properties of NdFeB magnets stem from their chemical composition and the precise manufacturing techniques used to produce them. They are available in various grades, each offering different levels of magnetic performance and temperature resistance.
How Are NdFeB Magnets Made?
The production of NdFeB magnets involves several key steps, each critical to achieving their exceptional magnetic properties. Here’s a detailed look at the process:
1. Raw Material Preparation
The production begins with the preparation of raw materials, including neodymium, iron, and boron. These elements are combined to form the NdFeB alloy. Additional elements like dysprosium and praseodymium may be added to enhance corrosion resistance and coercivity.
- Neodymium: A rare earth element that provides the magnet’s strength.
- Iron and Boron: These elements contribute to the magnet’s structure and durability.
The raw materials are melted in a furnace to form a homogeneous alloy.
2. Powdering the Alloy
Once the alloy is formed, it is cooled and broken down into a fine powder. This step is crucial for shaping the magnets and aligning their magnetic domains. The powdering process involves:
- Hydrogen Decrepitation: Hydrogen gas is used to break the alloy into smaller pieces.
- Grinding: The pieces are ground into a fine powder with uniform particle size.
The resulting NdFeB powder is highly reactive and must be handled carefully to prevent oxidation.
3. Pressing and Sintering
The powdered material is pressed into molds to create the desired shape. This step is followed by sintering, where the pressed material is heated in a vacuum or inert atmosphere to fuse the particles together. Sintering enhances the magnet’s density and mechanical properties.
- Sintered NdFeB Magnets: These magnets offer superior magnetic performance and are widely used in high-tech applications.
4. Magnetization
After sintering, the magnets are exposed to a strong magnetic field to align their magnetic domains. This step gives the magnets their permanent magnetic properties.
What Materials Are Used in NdFeB Magnet Production?
The primary materials used in NdFeB magnet production include:
Material | Role in Magnet Production |
Neodymium | Provides high magnetic strength. |
Iron | Enhances structural integrity. |
Boron | Stabilizes the crystalline structure. |
Dysprosium | Improves temperature resistance. |
Praseodymium | Enhances corrosion resistance. |
These materials are carefully combined to achieve the desired magnetic and mechanical properties.
Why Are NdFeB Magnets So Strong?
The strength of NdFeB magnets comes from their unique crystalline structure and high magnetic flux density. The Nd2Fe14B structure allows for exceptional magnetic energy per unit volume, making these magnets the strongest commercially available.Compared to other magnets like ferrite magnets or alnico magnets, NdFeB magnets offer:
- Higher Magnetic Strength: Ideal for compact applications.
- Better Energy Efficiency: Used in wind turbines and electric vehicles.
- Versatility: Suitable for a wide range of industries.
What Is the Role of Recycling in NdFeB Magnet Production?
Recycling plays a crucial role in reducing the environmental impact of NdFeB magnet production. Spent NdFeB magnets and magnet scrap are processed to recover valuable materials like neodymium and dysprosium. The recycling process involves:
- Hydrogenation: Breaking down used magnets into a fine powder.
- Separation: Extracting rare earth elements from the powder.
- Reprocessing: Using the recovered materials to produce new magnets.
Recycling not only conserves resources but also reduces the reliance on rare earth mining, which can have significant environmental consequences.
How Are NdFeB Magnets Used in Modern Industries?
NdFeB magnets are indispensable in many industries due to their strength and compact size. Here are some key applications:
1. Automotive Industry
- Electric Vehicles (EVs): Powering efficient motors.
- Hybrid Vehicles: Supporting sustainable transportation.
- Autonomous Driving Systems: Enhancing sensor performance.
2. Renewable Energy
- Wind Turbines: Generating clean energy with high efficiency.
- Wave Energy Generators: Capturing ocean energy.
3. Consumer Electronics
- Speakers and Headphones: Delivering high-quality sound.
- Mobile Devices: Compact components for modern gadgets.
4. Medical Devices
- MRI Machines: Creating strong magnetic fields for imaging.
- Surgical Tools: Assisting in precision operations.
For customized solutions, visit Customized NdFeB Magnets.
NdFeB Enabling Innovations
Visit about us page to learn more about NdFeB magnet production.
What Are the Challenges in NdFeB Magnet Production?
Despite their advantages, NdFeB magnets face several challenges:
- Temperature Sensitivity: Performance decreases at high temperatures.
- Corrosion: Requires protective coatings like nickel or PTFE.
- Resource Dependency: Relies on rare earth elements, which are limited in supply.
Innovations in recycling and alloy development are addressing these challenges, ensuring a sustainable future for NdFeB magnets.
What Does the Future Hold for NdFeB Magnets?
The future of NdFeB magnets looks promising, with advancements focusing on:
- Improved Recycling Techniques: Reducing environmental impact.
- Enhanced Alloys: Increasing temperature resistance and durability.
- Broader Applications: Expanding into aerospace and space exploration.
These developments will ensure NdFeB magnets remain at the forefront of technological innovation.
Key Takeaways: The Production of NdFeB Magnets
- Strongest Permanent Magnets: Compact and highly effective.
- Complex Production Process: Involves alloying, sintering, and magnetization.
- Recycling Is Crucial: Reduces environmental impact and conserves resources.
- Wide Applications: From electric vehicles to medical devices.
- Future Innovations: Focused on sustainability and performance.
For tailored solutions, explore Customized NdFeB Magnets.
Welcome to our factory’s custom NdFeB magnet services, where your ideas and needs become reality.
Simply share your concepts, requirements, or design drawings, and we’ll work closely with you to produce high-quality NdFeB magnets tailored to your exact specifications and performance standards.
You’ll benefit from competitive pricing, complimentary samples, and professional technical support from our dedicated team, making the customization process worry-free, safe, and cost-effective.
Our goal is to ensure that your products achieve outstanding performance with the highest level of quality and precision.
Economic Development Zone, Industrial Park, Shehong City, Sichuan Province, China.
Contact
News
US Department of Defense Allocates $5.1 Million to Recover Rare Earths from E-Waste
On January 17, 2025, the US Department of Defense announced a $5.1 million allocation to Rare Resource Recycling Inc. under the Defense Production Act.
China Revises and Implements the “Regulations for Outward Direct Investment Statistics,” Including Rare Earth Oxides
It is reported that on January 1, 2025, the Ministry of Commerce, the National Bureau of Statistics, and the State Administration of Foreign Exchange officially implemented the revised “Regulations for Outward Direct Investment Statistics.”
Canada Rare Earth Acquires Majority Stake in Laos Rare Earth Refinery
According to Magnet Materials News, on January 9, 2025, Canada Rare Earth Corp. announced plans to acquire a 70% stake in a rare earth refinery in Laos. This acquisition aims to enhance supply security and economic benefits.