How Are Neodymium Magnets Made? A Step-by-Step Guide to the Manufacturing Process
But how exactly are these strong magnets made? Understanding the manufacturing process of neodymium magnets not only highlights their importance but also explains the meticulous steps involved in creating these versatile magnetic materials.In this article, we’ll break down the entire process of how neodymium magnets are made, touching on the materials, techniques, and technologies involved.
Whether you’re an engineer, a student, or simply curious about the science behind magnets, this guide will provide a comprehensive and easy-to-understand explanation of the topic.
Table of Contents
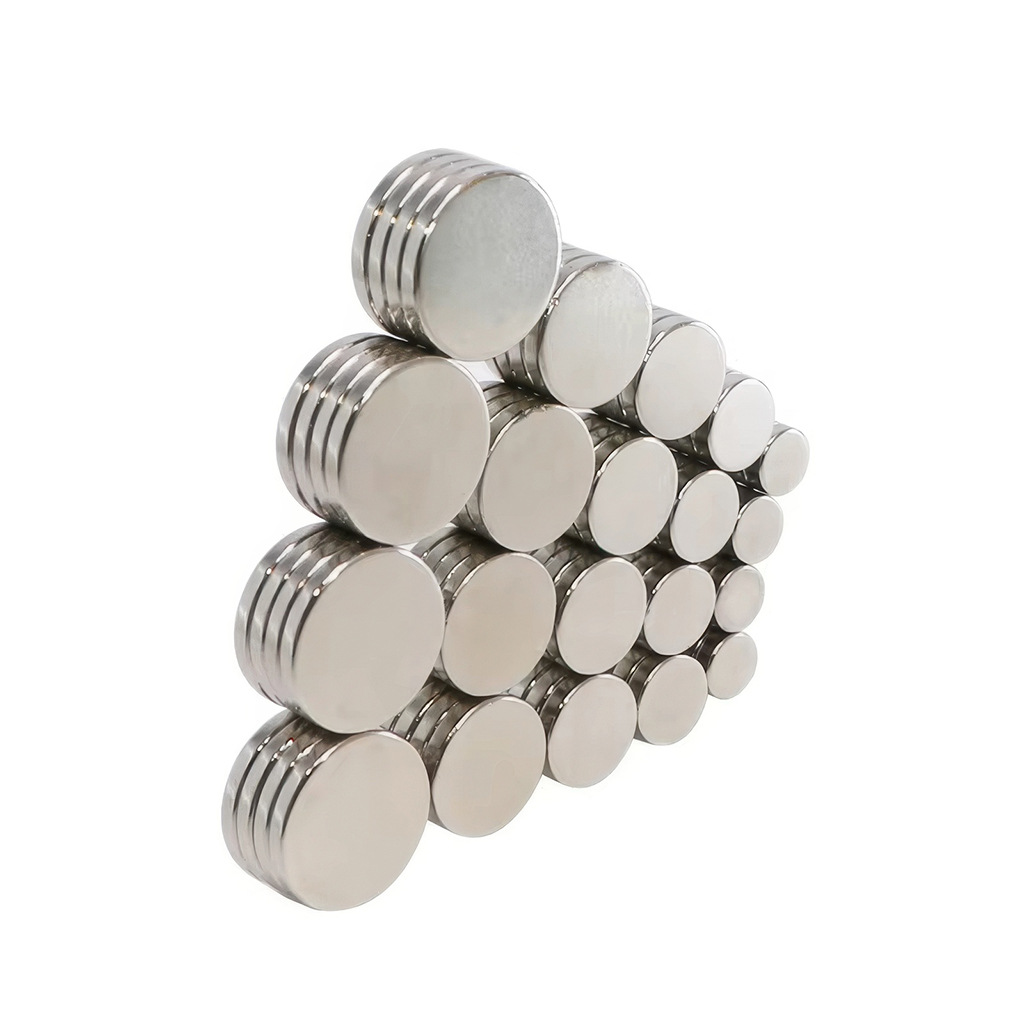
What Are Neodymium Magnets Made Of?
Neodymium magnets are a type of rare earth magnet, made primarily from a combination of neodymium, iron, and boron. This composition is often referred to as NdFeB, which stands for neodymium, iron, and boron.
Key Materials in Neodymium Magnets:
- Neodymium (Nd): A rare earth element that provides the high magnetic strength.
- Iron (Fe): A common metal that adds structural integrity and contributes to the magnet’s overall strength.
- Boron (B): Enhances the magnet’s stability and resistance to demagnetization.
Other elements, such as dysprosium and nickel, may also be added to improve the magnet’s performance in high-temperature environments or to provide protective coatings against corrosion.
The Step-by-Step Manufacturing Process of Neodymium Magnets
The production of neodymium magnets involves several precise and carefully controlled steps. Each stage plays a crucial role in ensuring the magnet’s magnetic properties, durability, and quality.
1. Melting the Raw Materials
The process begins with melting the raw materials, including neodymium, iron, and boron, in a vacuum induction furnace. This furnace operates in an inert atmosphere, typically using argon gas, to prevent contamination of the materials. The ingredients are melted together at a high melting point, forming a liquid magnetic alloy.
2. Rapid Cooling Process
After melting, the molten material undergoes a rapid cooling process to form a solidified structure. This step is crucial as it ensures the formation of fine magnet particles with the desired magnetic properties. The material is cooled to form thin flakes or blocks, depending on the manufacturing requirements.
How Are the Magnet Particles Processed?
3. Jet Milling and Particle Refinement
Once the material has solidified, it is crushed into smaller pieces and ground into a fine powder using a jet mill. This process ensures that the particles are refined to a size of just a few microns, improving the magnet’s strength and consistency.
- Why is this important? The smaller the particles, the better the magnetic domains align during the subsequent steps, resulting in higher magnetic properties.
4. Aligning the Magnetic Domains
The powder is then placed in a strong magnetic field, which aligns the magnetic domains in the same direction. This step is crucial for achieving the desired preferred direction of magnetization, which determines the magnet’s final performance and strength.
What Is the Sintering Process?
5. Pressing the Powder into Compact Shapes
The aligned powder is compacted into a desired shape and size using an isostatic press. During this stage, the mixture is pressed into blocks, discs, or plates that resemble the final product.
6. Sintering and Bonding
The compacted shapes are heated in a sintering process, which bonds the particles together to form a solid sintered magnet. This process involves heating the material to just below its melting point, ensuring that the particles fuse without losing their magnetic properties.
How Are Neodymium Magnets Finished?
7. Machining and Shaping
After sintering, the magnets are still rough and must be refined to their final shape and size. This is done using precision machines that grind and polish the magnets. The machine process ensures that the magnets are very hard, durable, and ready for their intended applications.
- Pro Tip: Magnets are often shaped into blocks, rings, or cylinders, depending on their use in industries like automotive, wind power, or electronics.
How Are Neodymium Magnets Protected?
8. Coating and Corrosion Resistance
To protect against corrosion, the magnets are coated with materials such as nickel or PTFE (Teflon). The choice of coating depends on the application, with some magnets requiring additional resistance to moisture or high temperatures.
The Final Steps in Magnet Manufacturing
9. Magnetization
The final step in the production process is magnetization, where the magnets are exposed to a strong coil of wire that generates a magnetic field strength sufficient to permanently magnetize the material. At this stage, the direction of the magnetism is locked, ensuring that the magnet matches the direction required for its application.
10. Quality Control and Customization
Before being shipped, the magnets undergo rigorous quality control to ensure they meet specific requirements for grade or strength, shape, and magnetic performance. Some manufacturers offer customized neodymium magnets with tailored properties for specialized industries.For example, you can explore options for custom NdFeB magnets here.
Applications of Neodymium Magnets
Neodymium magnets are used in a wide range of industries, including:
- Electronics: Smartphones, speakers, and hard drives.
- Automotive: Electric motors and hybrid vehicles.
- Wind Power: Permanent magnet generators in wind turbines.
- Medical Devices: MRI machines and surgical tools.
- Industrial Equipment: Motors and servo systems.
For more information on customized magnets for specific industries, visit the NdFeB Magnets Factory.
Summary of the Neodymium Magnet Manufacturing Process
- Raw Materials: Mainly neodymium, iron, and boron.
- Melting and Cooling: Ingredients are melted in a vacuum induction furnace and rapidly cooled.
- Particle Refinement: Ground into fine micron-sized particles using a jet mill.
- Magnetic Alignment: Aligned in a strong magnetic field.
- Sintering: Heated and bonded to form solid sintered magnets.
- Shaping and Coating: Machined to the final shape and size, then coated for protection.
- Magnetization: Exposed to a strong magnetic field to lock the direction of magnetism.
- Quality Control: Tested for magnetic performance and customized as needed.
For more insights and options, check out the Customized Neodymium Magnets page.
Neodymium magnets are a marvel of modern technology, combining precise engineering and advanced materials to create the strongest permanent magnets available. Whether you’re designing cutting-edge electronics or building renewable energy solutions, understanding the manufacturing process helps you appreciate the science and craftsmanship behind these powerful magnets.
Welcome to our factory’s custom NdFeB magnet services, where your ideas and needs become reality.
Simply share your concepts, requirements, or design drawings, and we’ll work closely with you to produce high-quality NdFeB magnets tailored to your exact specifications and performance standards.
You’ll benefit from competitive pricing, complimentary samples, and professional technical support from our dedicated team, making the customization process worry-free, safe, and cost-effective.
Our goal is to ensure that your products achieve outstanding performance with the highest level of quality and precision.
Economic Development Zone, Industrial Park, Shehong City, Sichuan Province, China.
Contact
News
US Department of Defense Allocates $5.1 Million to Recover Rare Earths from E-Waste
On January 17, 2025, the US Department of Defense announced a $5.1 million allocation to Rare Resource Recycling Inc. under the Defense Production Act.
China Revises and Implements the “Regulations for Outward Direct Investment Statistics,” Including Rare Earth Oxides
It is reported that on January 1, 2025, the Ministry of Commerce, the National Bureau of Statistics, and the State Administration of Foreign Exchange officially implemented the revised “Regulations for Outward Direct Investment Statistics.”
Canada Rare Earth Acquires Majority Stake in Laos Rare Earth Refinery
According to Magnet Materials News, on January 9, 2025, Canada Rare Earth Corp. announced plans to acquire a 70% stake in a rare earth refinery in Laos. This acquisition aims to enhance supply security and economic benefits.