Comprehensive Guide to Protective Coatings for Neodymium Magnets
In this article, we’ll explore why coatings for neodymium magnets are critical, the types available, and how to select the best option for your specific application.
Table of Contents
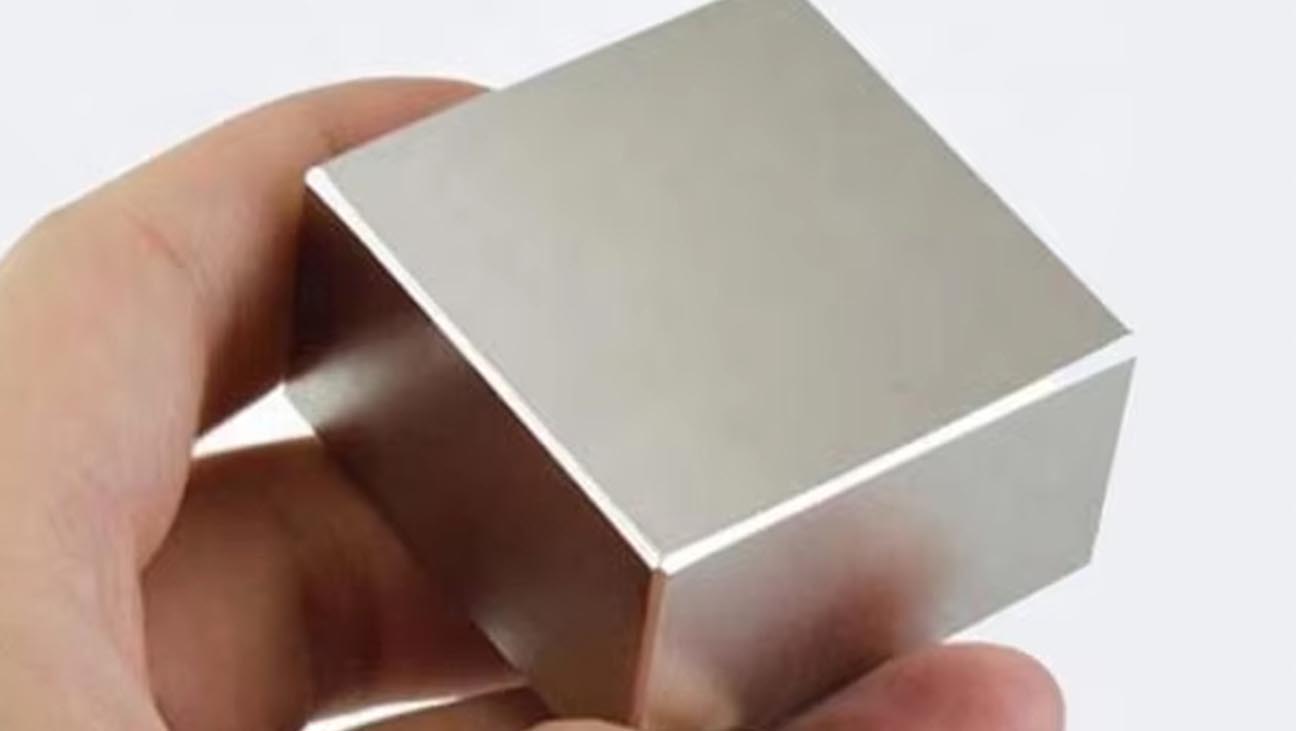
Why Do Neodymium Magnets Need Coatings?
Neodymium magnets, also called NdFeB magnets, are composed of neodymium, iron, and boron. While their magnetic performance is unmatched, the iron content makes them highly susceptible to corrosion when exposed to humidity, oxidation, or other harsh environmental factors. Without a protective coating, the surface of the magnet can degrade, leading to reduced function or complete failure.Coatings act as a protective layer, shielding the magnet’s surface from environmental damage while sometimes enhancing its corrosion resistance and aesthetic appeal. That’s why all neodymium magnets come with some form of coating tailored to their specific use case.
The Importance of Coatings for Neodymium Magnets
Why are coatings so crucial for permanent magnets like neodymium? Here are the key benefits:
- Corrosion Protection
Neodymium magnets are prone to corrosion, especially in outdoor applications or environments with high humidity. Coatings prevent the magnet from deteriorating and ensure longevity. - Increased Durability
Coatings add a layer of protection that reduces the risk of wear and tear, particularly for magnets in the automotive industry, medical devices, or industrial equipment. - Enhanced Aesthetic Appeal
Some coatings, like gold plating, are chosen for their decorative properties, making magnets suitable for applications requiring a polished appearance.
How Does Corrosion Affect Neodymium Magnets?
Corrosion is a significant concern for NdFeB magnets. When exposed to moisture, the iron within the magnet oxidizes, leading to rust and structural disintegration. Over time, this can weaken the magnet’s strength or render it entirely unusable. For instance, sintered neodymium magnets are especially vulnerable, as their porous structure allows moisture to penetrate easily.In extreme cases, corrosion can occur within 24 hours of exposure to a hostile environment. This highlights the necessity of selecting a proper protective coating to mitigate these risks.
Types of Coatings for Neodymium Magnets
Choosing the right coating for neodymium magnets depends on the application and operating environment. Below are the most commonly used types of coatings:
Coating Type | Features | Applications |
Nickel (Ni-Cu-Ni) | Offers excellent corrosion resistance and durability; commonly used. | Ideal for general-purpose magnets. |
Zinc Coating | Economical option with moderate corrosion protection. | Suitable for indoor applications. |
Epoxy Coating | Provides a thick, durable layer; resistant to harsh environments. | Used in outdoor applications or medical. |
Teflon Coating | Ensures excellent chemical resistance and a smooth finish. | Ideal for medical devices and food-safe. |
Parylene Coating | Highly resistant to chemicals, moisture, and extreme conditions. | Critical for aerospace and electronics. |
Gold Coating | Thin layer for decorative purposes; offers limited durability. | Used in luxury products or jewelry. |
How to Select the Right Coating for Your Application
When selecting the right coating for your magnet, consider the following factors:
- Environmental Conditions
Magnets used in outdoor applications or high-humidity environments require robust coatings like epoxy or nickel plating to withstand moisture and corrosion. - Application-Specific Needs
For medical devices, coatings like Teflon or Parylene offer excellent chemical resistance and safety. In contrast, industrial magnets may prioritize durability over aesthetics. - Budget Constraints
While coatings like gold or Parylene are more expensive, options like zinc or nickel provide cost-effective protection for less demanding applications. - Magnet Size and Shape
Complex shapes may require specialized coatings to ensure uniform coverage and optimal performance.
Common Applications of Coated Neodymium Magnets
The versatility of coated magnets makes them suitable for a wide range of industries, including:
- Automotive Industry: Used in electric vehicles, powertrain systems, and autonomous driving technologies.
- Renewable Energy: Essential for wind turbines and tidal energy generators.
- Medical Devices: Found in MRI machines and other healthcare equipment.
- Household Appliances: Used in energy-saving motors and major appliances.
- Aerospace: Critical in electric propulsion systems and advanced aerospace engines.
Maintaining Coated Magnets for Longevity
To maximize the lifespan of your coated magnets, follow these maintenance tips:
- Avoid Abrasion
Repeated contact or friction can wear down the protective layer, especially in nickel-coated magnets. - Store Properly
Store magnets in a dry, temperature-controlled environment to prevent degradation. - Regular Inspections
Check for signs of wear or damage to the surface treatment and replace magnets as needed.
Questions to Consider When Choosing Magnet Coatings
What Happens if Magnets Are Left Uncoated?
Uncoated magnets are highly susceptible to corrosion, particularly when exposed to moisture or harsh environments. This can compromise their magnetic performance and structural integrity.
What Are the Best Coatings for Harsh Environments?
For applications exposed to temperature and humidity, epoxy coatings or parylene coatings are ideal, as they offer excellent corrosion protection and resistance to wear.
Are Coated Magnets Suitable for Medical Use?
Yes, coatings like Teflon and Parylene are biocompatible and safe for medical devices, ensuring both functionality and patient safety.
Advantages of Coated Neodymium Magnets
Coated magnets offer several advantages, including:
- Enhanced Corrosion Resistance: Protects against rust and degradation.
- Improved Durability: Extends the lifespan of magnets used in demanding applications.
- Versatility: Adaptable to industries ranging from aerospace to household appliances.
- Aesthetic Appeal: Ideal for visible or decorative applications.
Why Choose Customized Neodymium Magnets?
For specialized applications, opting for customized neodymium magnets ensures that the coating thickness, material, and performance meet your unique requirements. Learn more about customized NdFeB magnets here.
Closing Thoughts
Protecting your neodymium magnets with the right coating is vital for ensuring their longevity, performance, and resistance to environmental factors. By understanding your needs and the available options, you can select the best surface treatment that not only enhances durability but also meets your specific application requirements.
Key Takeaways
- Neodymium magnets require coatings to prevent corrosion and maintain performance.
- Common coatings include nickel, epoxy, zinc, Teflon, and Parylene.
- Choose coatings based on environmental conditions, application, and budget.
- Proper storage and maintenance ensure the longevity of your coated magnets.
- Explore customized NdFeB magnets for tailored solutions.
This article highlights the importance of protective coatings for neodymium magnets while offering practical tips and insights for selecting the best options. Let us know your requirements, and we’ll help you find the perfect solution for your magnetic needs!
Welcome to our factory’s custom NdFeB magnet services, where your ideas and needs become reality.
Simply share your concepts, requirements, or design drawings, and we’ll work closely with you to produce high-quality NdFeB magnets tailored to your exact specifications and performance standards.
You’ll benefit from competitive pricing, complimentary samples, and professional technical support from our dedicated team, making the customization process worry-free, safe, and cost-effective.
Our goal is to ensure that your products achieve outstanding performance with the highest level of quality and precision.
Economic Development Zone, Industrial Park, Shehong City, Sichuan Province, China.
Contact
News
US Department of Defense Allocates $5.1 Million to Recover Rare Earths from E-Waste
On January 17, 2025, the US Department of Defense announced a $5.1 million allocation to Rare Resource Recycling Inc. under the Defense Production Act.
China Revises and Implements the “Regulations for Outward Direct Investment Statistics,” Including Rare Earth Oxides
It is reported that on January 1, 2025, the Ministry of Commerce, the National Bureau of Statistics, and the State Administration of Foreign Exchange officially implemented the revised “Regulations for Outward Direct Investment Statistics.”
Canada Rare Earth Acquires Majority Stake in Laos Rare Earth Refinery
According to Magnet Materials News, on January 9, 2025, Canada Rare Earth Corp. announced plans to acquire a 70% stake in a rare earth refinery in Laos. This acquisition aims to enhance supply security and economic benefits.